1.
A consideration of cavity layouts
1) Use balanced layouts as much as possible.
2) Make cavity layouts and pouring gates' settings symmetrical so as to prevent partial loads due to the uneven force of the
molds, resulting in flash overflow problem.
3) Compact mold cavity layout to reduce the molds' sizes.
2.
A consideration of flow guidance
1) We can successfully make the molten plastic fill the
mold cavities, not generating eddies and being able to exhaust smoothly.
2) Try to prevent the plastic melt glues directly beating the mold cores with small diameters and metal inserts in order to avoid core shifts or deformations.
3.
Considerations of heat dissipation and pressure drop
1) Heat loss and pressure drop should be as little as possible.
2) The flow paths should be short.
3) The flow cross-sectional area should be big enough.
4) Bending flow paths and sudden change of the flow direction should be avoided.
5) The surface roughness should be low when we process the runners.
4.
A consideration of flow balance
1) When we fill the multi-cavities, the runners should be balanced; try to make the molten
plastic fill every cavity at the same time so as to ensure the consistency of every mold's quality.
2) We should adopt naturally-balanced layouts for sub-runners.
3) If the runners can not be naturally balanced, we can adopt manual balance method.
5.
A consideration of waste
Under the premise of smooth filling without affecting the flow and pressure loss, reduce the runners' volumes (length or cross-sectional area) in order to decrease the waste of runners and recycling costs.
6.
A consideration of cold charges
We need to design appropriate cold slug wells or flash grooves to prevent cold charges directly going into the
mold cavities and affecting the filling quality.
7.
A consideration of exhaust
We should smoothly make the molten plastic fill the mold cavities and the air in the mold cavities smoothly go away in order to prevent the problem of charring.
8.
A consideration of finished products' quality
1) Avoid problems of short shots, burrs, flow marks, jet flows, residual stresses, etc.
2) Under the circumstances of runner systems' long flow paths or multiple gating, we need to prevent buckling deformation problem of the finished products due to unbalanced flow, insufficient pressure holding or uneven shrinkage.
9.
A consideration of production efficiency
Try to minimize the required post-processing as much as possible to shorten the forming cycle, and to increase production efficiency.
10.
A consideration of ejection positions
We need to consider appropriate ejection positions to avoid deformations of finished products when they are demoulded.
11.
A consideration of plastic materials
We should choose plastic with high viscosity or relatively short L/t, and avoid using runners with too long length or small sizes.
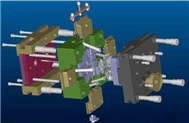