Several commonly used plastic materials for toys are polystyrene and modified polystyrene which is also known as high-impact polystyrene. The two materials can be mixed for injection molding. The more the GPPS composition is, the better the surface gloss and fluidity become. The other polystyrene modifier in toy plastic parts is MBS (polymethyl methacrylate-styrene copolymer), which is transparent
ABS. The composition of butadiene-styrene polymer makes surface hardness of the product higher; wear resistance and heat resistance are improved. The butadiene in toy plastic parts enhances flexibility of the material and maintains the toughness, elasticity and impact strength of the material; styrene maintains good formability (fluidity and colorability) and rigidity of the material. Blending butadiene-styrene polymer with PVC can improve the toughness, durability and aging resistance of the material. Mixing butadiene-styrene polymer with PC can improve impact strength and heat resistance.
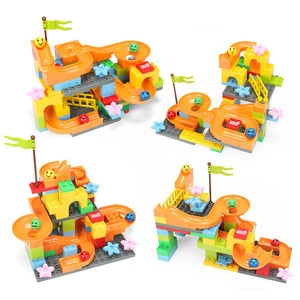
The molding temperature range of
toy plastic parts is narrow, and the thermal stability is poor. The formaldehyde monomer decomposes above 250°C. The color of the melt becomes darker. It is harmful and ineffective to increase the temperature alone to improve the fluidity. In ordinary injection molding, low barrel temperature and short residence time should be used to increase the injection pressure and improve the fluidity of the melt and surface quality of the product.
The molding shrinkage rate of
toy plastic parts is great and the plastic part is easy to shrink, so it is necessary to extend the heat preservation time to supplement. Polyethylene is divided into high density HDPE and low density HDPE. As the density increases, the transparency decreases. Polyethylene is insoluble in any solvent at room temperatures and its surface is easily scratched.
Polypropylene for toy plastic parts has better surface scratch resistance than than of polyethylene, good chemical stability, being insoluble in organic solvents and difficult to thermoprint and bond. The molding shrinkage rate is great, and shrinkage cavity is easy to appear, so longer pressure holding time should be adopted for feeding. Polycarbonate has the best impact resistance.
Toy plastic parts need to be fully dried before injection molding, and there are special requirements for mold temperature control, generally 80℃ to 100℃. After molding, annealing treatment can be used in order to reduce internal stress, and annealing temperature is bewteen 125℃ to 135℃; annealing time is 2h, and then naturally cool to room temperature. Polyamide is commonly known as nylon. Nylon materials cannot be colored, such as oil injection and pad printing, and they must be dried before injection. Since the plastic parts for toys are prone to internal stress after molding, annealing and humidity control are required. Annealing conditions: the temperature should be from 10℃ to 20℃ higher than the use temperature; the time depends on the thickness of the product, generally about 10 to 60 minutes. Humidity control conditions: soak in boiling water or potassium acetate solution for 2 to 6 hours. Polymethyl methacrylate is organic glass, commonly known as acrylic fibers, which has the strongest light conductivity among plastics.
Requirements for toy plastic parts
The overall design requirements for toy plastic parts: the drawings should be standardized, and the references to the same icon annotations in the drawings should be unified. The purchased parts manually produced before mold opening should be stocked common parts or national standard parts.
If the color of the product appearance of a certain part is different, first consider disassembling, and then perform 4 items such as oiling, silk screen and labeling. In addition to the appearance required by customers, the design of plastic parts should also consider the production of molds. The accuracy of molds and sizes of parts mainly depend on the accuracy of molds and sizes of parts.
The demolding slope of toy plastic parts: generally, hard rubber parts must be designed along the demolding direction with sufficient demolding slopes. Wall thickness of plastic parts: the wall thickness of the same plastic part should be the same. Otherwise, the gradual change principle should be adopted. However, it should not exceed 1.5 to 2 times the size of wall thickness. Rounded corners or rounded edges: in the molding process of plastic parts, the structure of toy plastic parts should be as smooth as possible.
In terms of the performance of
toy plastic parts, the surface of the plastic parts should be as smooth as possible to reduce potential hazards of products and stress concentration at sharp corners as well as sharp edges. Surface finishment and surface patterns: generally speaking, the surface finishment of the mold should be one level higher than that of the plastic part. If there is no requirement for the surface finishment of plastic parts, it is recommended that brain patterns should be chosen to improve the molding quality of plastic parts.
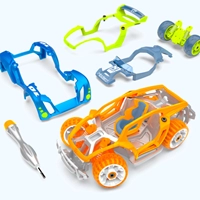
The material thickness of
toy plastic parts is 0.5 to 0.6 times the size of the wall thickness; the transition fillet between the steel bar and wall should be 0.25 times greater than the size of wall thickness, and the height of the stiffener should not exceed 3 to 10 times the size of the wall thickness; the end face of the stiffener should be completely rounded to reduce its own pressure.
If there is no special requirement, single lip and single-side outlet structure should be adopted; the lip size is from 0.3 to 0.5mm; for ultrasonic components or other rubber parts with high matching requirements, double lips should be selected. There are through holes and blind holes for toy plastic parts. The distance between two holes should be at least 2 times the size of the hole diameter; hole edges and parts should be 3 times as big as the hole diameter.
The hole for toy plastic parts should not be too deep, especially for blind holes, usually less than or equal to1.5 and should be 2 times less than the diameter.
In addition to positioning and limiting, the threaded posts of
toy plastic parts are mainly used to fasten two or more separate parts together; the mold industry has a standard series of products, namely No. 15 screws. Anti-slip surfaces such as patterns and holes should be provided at the fusion of plastic parts to prevent different fastening forces between plastic parts and inserts.