1. Metal dust
In the normal stamping process of punching and blanking, the waste is clamped in the cavity of the die, and it falls from the blanking hole of the mold driven by the subsequent waste. However, when the suction force of the punch of the terrace mold to the waste is greater than the clamping force of the concave mold cavity to the waste, the waste will jump to the surface of the concave die driven by the upward movement of punches of terrace molds, resulting in the waste rising. The main reason is that a vacuum is generated between the lower surface of the punch of the terrace mold and the waste in the stamping process, so that certain negative pressure is generated at the lower part of the waste, making the waste adsorb on the punch of the terrace mold, and the waste rises and forms dust.
Figure 1 is a schematic diagram of analyzing chip jumping from a mechanical point of view. Figure 1(A) shows the punch gets into the concave mold, and cuts off a piece of waste, forming dust. When the bite force f between the side wall of the blanking knife-edge and the powdered part is less than the adsorption force F received by the upper mold when it moves upwards in the production, as shown in Figure 1(B), the metal dust jumps out of the lower mold and enters the mold surface, As shown in Figure 1(C).
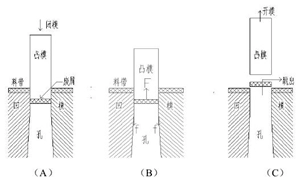
Figure 1 The diagram of metal chips
When the terrace mold takes the waste from the concave mold and it falls on the lower mold, the operator must clean up the waste on the mold before proceeding to the next punching. In this way, the labor time is directly increased and the production efficiency is reduced. As the speed of the stamping increases, the formed metal dust can easily cause production problems and seriously affect the appearance quality of the
stamping products. Figure 2 is an example of the product being damaged by metal dust. When the metal dust is severe, it will affect the accuracy of the mold's working parts, thereby affecting the service life of the mold.
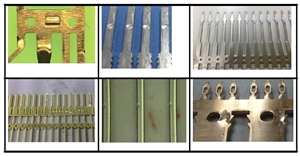
Figure 2 Examples of products being damaged by metal dust
Thoroughly prevent the jumping of waste materials, which is conducive to improving the quality of products and the smooth stamping.
2.
Analysis of the reasons for the generation of metal dust
Analysis of the causes of jumping chips in the mold design
The gap of the knife-edge being too big
The knife-edge clearance of blanking parts is shown in Figure 3. The unreasonable design clearance of the mold's knife-edge will affect normal production. If the gap is too big, metal dust will be generated. If the gap is too small, the material will be blocked and the mold will be damaged.
Figure 3 The knife-edge clearance of blanking parts
When the operation of the mold is very smooth, the inner surface of the part is worn due to the number of friction between the falling waste and the inner surface of the knife-edge part, resulting in a large knife-edge gap. Figure 4 shows a schematic diagram of the wearing of a part in the stamping process.
Figure 4 The wearing of the part in the stamping process
After the knife-edge parts are worn, the knife-edge gap increases, which is easy to produce metal dust.
The length of the punch getting into the knife-edge part is too long or too short, and the contact area between the punch and the material belt is too large.
Generally speaking, the length of the punch is equal to the thickness of the punch's fixing plate, stripping plate's backing plate, stripping plate, material and the length of the punch getting into the knife-edge part. If the length of the punch is too great, the material will start punching before the punch is pressed, which will easily cause the punch blade to wear, make the shape of the waste material irregular, materials jam, and the next punching waste stick to the surface of the material belt, resulting in damaging by metal dust. If the length of the punch is too short, the waste is not completely punched below the straight section of the knife-edge, and it is easy to be sucked by the adsorption force between the punch and knife-edge, resulting in metal dust. Figure 5 shows a schematic diagram of the length of the punch extending into the concave mold.
Figure 5 A schematic diagram of the length of the punch extending into the concave mold
The contact area between the punch and material belt is too big, and closed space is formed between the punch, waste and knife-edge, which is equivalent to a vacuum effect. When the punch rises, the suction force of the punch breaks the vacuum, generating negative pressure, and making the suction force of the punch greater than the friction of the knife-edge on the waste material, which has the same principle of a syringe, causes the waste material to be brought into the surface of the material and generates jumping chips.
Loosening of knife-edge parts
In the maintenance process, the knife-edge parts knock back and forth in the template, which accelerates the wear between the knife-edge parts and the template, causing a gap between the knife-edge parts and the template, and making the knife-edge parts loose. In this way, the knife-edge parts will move slightly in the template, resulting in uneven blanking gaps. The single side is too big or too small to bring waste onto the surface of the material and generate jumping chips. Figure 6 shows the schematic diagram of the gap between the part and template.
Figure 6 The gap between parts and template
Shapes and weights of the waste
Generally, the simpler the shape of the waste material is (such as round and square shapes), the more likely it is to produce jumping chips in the production process. The lighter the weight of the waste chip is, the more likely it is to produce jumping chips.
3.
Analysis of the causes of jumping chips in the manufacturing process
Too much punching oil or too viscous punching oil will easily cause chipping. The stamping oil used in the production has certain viscosity, which produces adhesion, and the waste was stuck to the punch. When the punch moves up from the material belt, the waste is taken from the concave mold, and the waste material left in the mold will cause damage to the product.
A new knife-edge just used in the manufacturing process or a newly repaired and polished knife-edge is more prone to chip jumping. In production, blanking is divided into two processes, namely cutting and tearing. The sharper the knife-edge is, the smaller the tearing surface becomes. The smoother the cutting surface is, the smaller the adhesion of the waste chip becomes, which makes it easier for the waste chip to jump from the mold.
For steel products, the friction produces magnetism due to the continuous reciprocating movement of the punch in the production, which produces a certain adsorption force to the waste, and the waste will adhere to the punch and be brought out from the concave mold, resulting in chip jumping.