The inner plate of the upper beam of the water tank of a certain project is shown in Figure 4. When the initial digital model (see Figure 4a) is produced in the selected stamping direction, there is a certain negative angle, and the production process cannot be realized. After the side angle of the bearing table is optimized (See Figure 4b), it can meet the secondary forming requirements without creating a new process. Confirm whether the structural shape and features of the stamping parts are conducive to ensuring the adequacy of its forming. Insufficient forming parts will have insufficient rigidity. Therefore, it is necessary to pay attention to the
auto parts with shallow drawing depth and flat parts without modeling features. You can increase the degree of deformation of the part by increasing features. Generally, CAE analysis software is used to confirm whether the stamping parts are sufficiently deformed.
Figure 4 Optimization of the draft angle of the inner plate of the water tank's upper beam
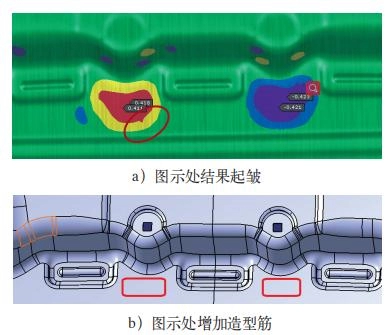
Figure 5 Wrinkled parts
Check whether there are parts with great changes in the shape of the stamping parts. An uneven force of the material may occur in the drawing process, resulting in instability of the material flow and partial wrinkles. Figure 6 is the style design of the front crossbeam of the top cover of a certain project. Because the shape of the front edge of the boss has a large step, the problem of wrinkling may occur after analysis. This can be solved by reducing the step difference between two adjacent parts.
Figure 6 The front crossbeam of the top cover
Quality assurance of parts
Check whether the easily rebounded stamping parts are designed to prevent a rebound in the structure. Beam parts and high-strength steel parts are prone to springback. Check if the stamping parts have features of preventing rebounding when designing the product. Whether characteristic ribs are added to prevent springback in the rounded corners or the sidewall of the part.
The distance between the edge of the hole and the end of the flanging filleted corner should not be too small to avoid deformation of the flanging and ensure the accuracy of the hole diameter after flanging.
The feasibility of strength of molds, trimming and punching processes
Check the nationality of the trimming line. The unreasonable position of the trimming line will lead to insufficient strength of the trimming block and affect the service life of the mold. As shown in the red circle in Figure 7a, the strength of the cutting edge cannot be guaranteed due to the great change in the shape of the edge line. As shown in the analysis in Figure 7b, the quality of the parts and mold will be affected. The edge line of the part can be optimized according to Figure 7c.
Figure 7 The optimization of strength of the cutting edge
The punching position should be rational.
Unreasonable punching position will result in insufficient strength of the pressing plate or the cutting edge of the lower die, which will affect the service life of the die. At the same time, the position of the hole should be set to ensure a reasonable space for the punch to avoid interfering the molded part in the punching process. The hole in Figure 8a is too close to the edge of the part, and the accuracy of the hole can't be ensured. At the same time, the negative flanging angle in Figure 8b interferes with the punch, and punching cannot be realized; the hole position needs to be moved inward.
Figure 8 The unreasonable punching hole
Costs of production
Estimate the size of the large stamping die in the planning stage, and optimize the shape or size of the part in combination with the machine table of the production site. Parts that do not meet the requirements for the selected production line should be adjusted in time. On the premise that the requirements for stamping, try to choose a machine tool with a lower cost.
On the premise of meeting the functional requirements and welding performance, ensure that the structure of the parts and the stamping process are simple and the mold structure is reasonable for the mounting plate, reinforced plate, and other parts in the structural parts. Meanwhile, minimize the number of molds. The part's structure can be guaranteed through methods such as reasonable layout, appropriate forming process, and compound die, improving utilization rates of materials of the whole vehicle.
Conclusion
1. Analyze the parts with cracks and wrinkles in the drawing and forming process, and eliminate the risk by optimizing the rounded corners and increasing the characteristic ribs; the characteristic of negative angles should be minimized for parts. The process can be achieved, and the number of molds should be minimized.
2. According to the material and shape of the parts, analyze possible risks such as springback, distortion and partial deformation, and carry out featured optimization and process prevention.
3. Ensure that the parts do not crack in the flanging process and the punching position is set reasonably. There is no interference in the production process or the mold strength is reduced due to the unreasonable hole distance. The deformation of the parts should be reduced.
4. The setting of the part's shape should consider factors such as improving utilization of materials, reducing the number of molds, simple structure and reasonable production line, and reducing production costs.