The in-vitro infrared thermometer is the mainstream product for rapid human body temperature measurement on the market. It is popular among users for its fast and accurate temperature measurement, digital display, and ease of viewing. To enhance user comfort,
overmolding thermometer casing uses two kinds of plastics. The overmolding process was developed from the secondary injection molding process. The implementation of the secondary injection molding process, combined with the structural characteristics of the injection molding machine, includes two methods: ① using double-nozzle injection molding machines ② using two single-nozzle injection molding machines. In the process of overmolding plastic parts, based on the characteristics of the materials, it can be divided into two scenarios: ① Two materials with different properties are combined by injection molding twice to obtain double-material molded plastic parts; ② The same material is dyed in different colors and combined by injection molding twice to obtain double-material molded plastic parts.
When using a double-nozzle injection molding machine, designing a mold for a double-material product requires setting up two fixed mold cavities of different shapes and two dynamic mold cores of the same structure for transformation and combination to obtain a double-material plastic part. Since the plastic parts using this method do not need to be removed from the injection molding machine during the injection molding process, the appearance of the plastic parts is refined and aesthetically pleasing. The thickness of the second material for the second molding on the plastic parts is generally 0.5 to 2 mm, which is costly and typically used for molding relatively small plastic parts. This process is commonly known as overmolding in the industry. When using two single-nozzle injection molding machines, two molds are required, and injection molding is performed twice on the two machines. In this process, after the first injection molding is completed, the plastic part is removed, placed on the second mold, and the second injection molding is performed on the second machine. The appearance of the plastic parts formed by this method is poor, requiring high-level injection molding technology, but the wall thickness can reach 3 mm, allowing the formation of larger part. Considering the overmolding requirements for a complete set of in-vitro thermometer casing plastic parts, this article presents a design for a overmolding mold, along with the accumulated experience and skills in overmolding design.
There are two complete sets of shell plastic parts for infrared thermometer products: the upper shell and the lower shell. The basic structure of the upper and lower shells has a mirror-symmetric relationship. The structure of the lower shell plastic part is illustrated in Figure 1. The dimensions of the plastic part are 195 mm × 171 mm × 30 mm. The plastic part is composed of two materials: a hard, thin-walled shell with an average wall thickness of 2 mm for the base, and a soft plastic encapsulation with a wall thickness of 1 mm on the outer surface of the base shell. The inner surface of the base shell includes features such as strip holes, ribs with a thickness of 1.2 mm, screw columns with an outer diameter of 0.6 mm, and a side groove on the left side. The plastic part uses two-color molding to achieve same-mold injection molding of a set of two shell parts. However, the adhesion between the hard plastic of the base shell and the soft plastic of the surface shell is poor, and the contact area between the two materials is small. Therefore, ribs must be added to the contact surface of the two materials to enhance adhesion and prevent detachment. The thickness of the selected hard plastic is ≥1 mm, and the thickness of the soft plastic is ≥0.8 mm. In this set of two-color plastic parts, the thickness of the base shell is set to 2 mm, and the thickness of the surface shell is 1 mm.
When overmolded plastic parts are created with different colors and materials, the first color molding forms the base hard shell, while the second color molding forms the surface soft shell. The possible materials for the base hard shell include polypropylene (PP), polystyrene (PS), acrylonitrile butadiene-styrene copolymer (ABS), polycarbonate (PC), and polyamide (PA). The possible materials for the surface soft shell include polyvinyl chloride (PVC), thermoplastic elastomer (TPE), and thermoplastic polyurethane elastomer (TPU). In the overmolding process, the base hard shell and the soft shell must have good compatibility. Additionally, the soft shell features wear resistance, durability, aesthetic appeal, comfort, waterproof sealing, a smooth non-sticky surface, and strength. For the plastic parts designed in this article, TPE is more suitable for the soft shell due to its good adhesion to PC, ABS, and PA. Therefore, PC+ABS is used for the base hard shell.
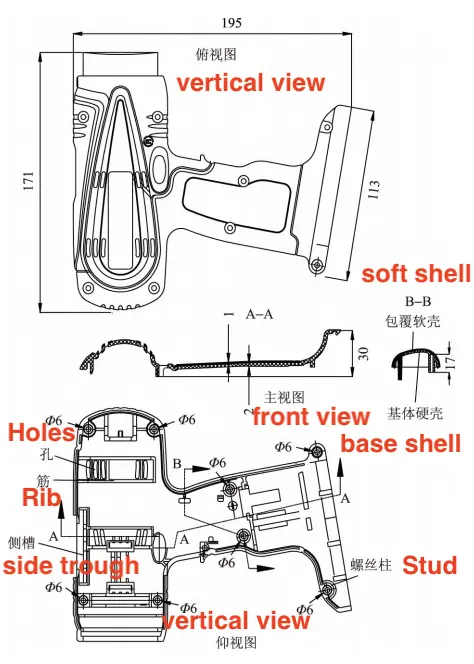
Figure 1 Upper shell of an infrared thermometer
The mold's working process is as follows:
Before the injection molding cycle begins, the mold is closed at the PL1 surface, and the first color barrel of the injection molding machine completes the injection of the two base hard shell cavities for the first molding. Simultaneously, the second color barrel of the injection molding machine remains closed, and the two second molding cavities have not yet been injected.
After step (1) is completed, the mold is opened, and the injection molding dynamic template rotation mechanism rotates the movable mold 180° counterclockwise around the mold's center axis O-O', then waits for mold closing.
The mold is closed again at the PL1 surface. After closing, the first color barrel of the injection molding machine completes the injection of the two first molding cavities, while simultaneously, the second color barrel completes the injection of the two second molding cavities. After the plastic parts cool, the mold is opened.
The mold is opened again, and the ejector mechanism of the second molding cavity activates, pushing ejector pin 37, drainage column ejector pin 27, and side gate pull rod 28 to eject the two-color plastic parts, as well as the first and second injection runner waste simultaneously. At this stage, the ejector mechanism of the first molding cavity remains inactive.
Reset spring 23 of the second molding cavity’s ejector mechanism resets the mechanism. After resetting, the dynamic template rotation mechanism rotates the movable mold 180° clockwise around the mold's center axis O-O’, and the mold is then ready for closing.
Injection molding cycle. After the mold completes step (5), the injection molding cycle from step (1) to step (5) begins again.
Before molding the two-color plastic part, attention must be paid to the following:
The gate position must be reserved and agreed upon with the product design company in advance.
② For large-area two-color overmolded plastic parts, the two key tests are drop tests and hot and cold shock tests. After a successful plastic part trial mold test, the first batch of samples must be verified through hot and cold shock tests. The test conditions are -40-65°C for 48 hours, after which mass production can begin.