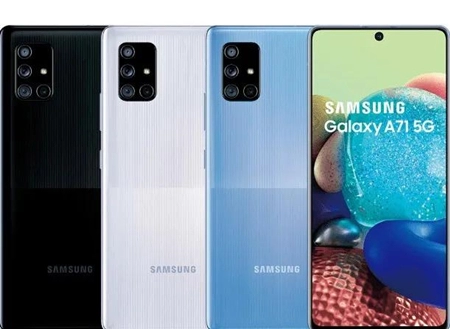
With the advent of the 5G, the demand for metal phone back cover has become less. Because of the massive MIMO technology adopted by 5G, a large amount of antennas need to be added to the phone, and metal will shield and interfere with the signal. The back cover of the phone not made of metal will be the general trend of the 5G era.
On 4G mobile phones, the plastic case has turned around with new technologies such as composite board molding and injection molded imitation glass to enhance the appearance and texture of the
phone cover. It has become the first choice for low-end and medium-end models because it is cost-effective, which is favored by Huawei, OPPO, VIVO and Samsung. Mobile phones with plastic back covers still occupy a certain market share in the 5G mobile phone market that occurs without interruption in the first half of 2020.
At present, the materials for back covers of mobile phones are shifting from metal into glass, ceramics and plastics. Among the three materials, glass and ceramics still have some problems due to their costs and processes, while plastics have favoured for back covers by the mobile phone manufacturer due to their easy processing and low costs.
Zirconia ceramics have the best wear resistance, brittleness, and shaping performance. They can be formed in one piece and have good colorability and high-end appearance, but their cost is the highest. The glass has good wear resistance and shaping performance, but its brittleness and coloring performance are not good. Its cost and appearance are average. The plastic has good toughness, not good wear resistance and rigidity, but its processing cost is low. Relatively speaking, plastics have the following incomparable advantages compared with ceramics and glass:
- The processing cost is low, and it cost not much for the user to replace the cover.
- There are a lot of colors and it is of vitality, which can effectively avoid many phones with the same cover.
- They have light weights. Nowadays, mobile phones are getting heavier and heavier, and the light weight of plastics will be well used.
- They are resistant to falling. Although the hardness of plastics is low and their ability to resist scratches is not excellent. Compared with glass, the characteristics of plastic materials not being broken after falling are quite good.
- Mobile phones with plastics have good signals, and the signal won't be blocked.
The plastic case used for 5G mobile phones is the development trend.
Judging from materials used for most mobile phone's back covers currently on the market, the metal back cover is gradually disappearing. The metal back cover has no problem with durability and texture. It mainly has a negative effect on the radio wave, and the metal will shield and interfere with the signal. Usually, metal shells should be used as little as possible for the 5G smartphones.
Many mobile phones with glass and ceramic back covers require a protective cover during use due to the fragile characteristics of glass and ceramic back covers. The materials of the protective cover are usually hard plastics such as ABS and PC. TPU soft plastics, leather and some special materials such as carbon fiber and bamboo have relatively high costs.
As for mobile phones with plastic back covers, composite plate imitation glass, IMT injection molding, and PC injection molding imitation 3D glass are adopted for back covers of mobile phones. The plastic shell has a qualitative leap in appearance and texture. At the same time, plastics have the characteristics of mature processing technology, low costs, and easy mass production, so they are favored by various manufacturers.
Materials and processing technology for the 5G mobile phone's plastic shell
3D composite plates
The core material of the 3D composite plate cover is the PC or PMMA composite plate. The 3D composite plate cover is also known as 3.5D, which is a composite plate made by co-extrusion of PC and PMMA. The structure of the plate is similar to a composite co-extruded film. The composite plate combines the high impact strength and bending resistance of PC as well as good hardness and wear resistance of PMMA, which improves the overall toughness of the material. The 3D composite plate has high definition, good gloss, good printability, and a good colorful glass effect can be obtained by the texture. The broken resistance is greatly improved after hardening, and there is no signal shielding, which can perfectly replace the glass for the back cover and screen of mobile phones. In the process of processing, PMMA with good hardness and wear resistance is generally used for the exterior, while PC with good toughness is used as the inner layer. There are three main forming methods, successively extrusion compounding, adhesiveness, and co-extrusion compound films. Each manufacturer chooses different forming methods according to the requirements for the product, such as thickness, appearance, hardness, flatness, etc.
The processes of 3D composite plates for phone shells are shown as follows: Composite extruded plates→Silk screen patterns→Transfer optical texture→Coating films→Silk screen patterns→High pressure forming→Surface hardening→CNC or laser cutting→Inspection