PC injection molding
In the evolution of the non metal mobile phone case, the plastic case has been upgraded with 3D imitation glass technology. Among them, the PC injection back cover and the middle frame integrated body stand out even more, that is, the integrated Unibody. The raw material is mainly PC. An injection molding press is adopted for the injection molding machine. The injection molding is stopped at the position accounting for 95%, and then the production is formed by pressing. A high-speed machine is adopted for the injection molding machine and it is good for the molding of thin-walled parts. Then, the subsequent processing is carried out after molding. The injection molding press process is mainly used to eliminate defects such as surface fogging, rainbow stress lines, and rubber injection rush lines during molding.
Precision injection compression molding, as an advanced form of injection molding, is more suitable for the molding of thin-walled transparent optical products. The injection compression molding PC back cover developed on the basis of the light guide plate can achieve the purposes of a series of treatments such as hardening, CNC machining and filming. The thickness and appearance can also achieve the aesthetic effect of good glass texture. In addition, injection molding also has the advantages of high efficiency, relatively simple process flow, and stable quality.
The injection molding compression process requires an injection molding machine with the injection compression function. However, the best of this kind of injection molding machine is a Japanese brand injection molding machine. The delivery cycle is long. The existing company which owns an injection molding machine with an injection compression function on the market is the company that manufactured light guide plates before, such as Kunshan Sanjing, Yidong Electronics, Jingermei Technology, Fulong Optics, Guangbao Mobile and so on.
The injection molding process of imitation glass is in the process of further development and maturity. With continuous breakthroughs in processing technology and promotion of terminals such as OPPO, Xiaomi, Samsung, Huawei and Vivo, mold injection and other related companies will benefit from it. At present, companies such as Sanjing, Tongda, Zhaoyi, Jierong, Yahan Optoelectronics, Xinhaoyuan, BYD and other companies have equipment with a similar principle to light guide plates.
The processes of making the shell by PC injection molding compression are as follows:
PC injection compression→Silk screen (pad printing) patterns→Exterior decoration→CNC→Surface hardening→Coating films→Assembly→Packaging
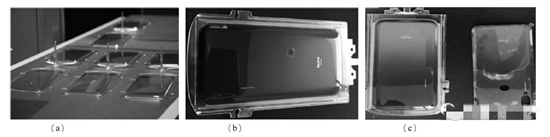
(a) Injection molded blanks
(b) Exterior decoration spray paint
(c) Parts after CNC machining
It should be noted that whether it is 3D composite board or PC injection molding compression, there are requirements for the processing environment; the constant temperature purified workshop must reach a standard of Level 10,000. The purified workshop with 100,000 refers to that the particles in the workshop are controlled within 100,000 per cubic meter. Meanwhile, there must be 5 to 10 Pa between the purified workshop and non purified workshop. Its purpose is to control particles on the production site.
Technical comparison
There is not much difference between the two processes in terms of appearance and texture. Therefore, the core of deciding which process to use is the cost. From the perspective of the processing cost of the back cover alone, the composite board is superior to the injection molding. The reasons are as follows: The composite board technology has been developed earlier (as early as 2017), and its processing flow is more mature; the overall yield rate is higher, reaching 98 to 99%. The high-pressure molding is adopted for the composite board, and the cost of its equipment is far lower than that of the current electric compression injection molding machine required for
PC injection molding. The mold's cost is also lower. Therefore, the cost is very low for each workpiece. As for the scratch resistance of plastics that everyone is concerned about, the composite board can generally achieve 4 to 5H, while the injection molding PC can only reach 2H. Moreover, the composite board has a high hardening yield.
However, in the mass production and the overall mobile phone accessories, the advantages of PC injection molding are reflected. This is because that the injection molding process can achieve super big R angles, for example, the popular large curved back cover and convex structure at the camera crater, which can be easily achieved by injection molding. More importantly, the integrated injection molding can achieve the complex buckle structure of the back cover and the middle frame, which can reduce the overall processing cost. Although injection molding PC has a disadvantage in hardening, the hardness of 2H can meet the demand for mass production. In addition, the choice of materials for the injection back cover is diversified. Both optical grades PMMA and nylon can be selected. Then, the hardness will no longer be a problem. As for the texture, printing ink can be chosen for injection molding. Although there is a certain compromise in the effect, the cost is greatly reduced. The biggest advantage of injection molding lies in mass production. Injection molded parts with better stability will have a significant cost reduction when mass production is carried out.