Abstract: Currently, complex sheet metal components in aerospace are primarily produced using drop forming or composite forming processes based on drop forming, leading to unstable part quality and low production efficiency. To address this, a specific double-curvature frame component with reinforcement grooves was selected for study. Three stamping schemes were developed based on variations in blank holder and blank shapes. Each scheme was analyzed and optimized using finite element simulation software, resulting in the selection of a blank holder with a perforated sheet as the preferred forming method. Corresponding tooling was designed, and testing with trial parts and minor mold adjustments confirmed that the formed components met surface quality and dimensional requirements for delivery. This approach enabled successful mass production and provides a valuable reference for optimizing similar parts and advancing traditional processes.
Lightweighting has always been a key focus of research and development in the aerospace industry. Thin-walled, high-strength sheet metal components are widely used in aircraft, based on the design principles of lightweight and strong structures. To minimize the aircraft's resistance during flight, the various load-bearing components must be enclosed within the external streamlined skin. As a result, a large number of sheet metal components with complex shapes and surfaces are found inside the aircraft. These sheet metal components are typically processed using rubber forming and drop forming. The rubber forming process is primarily used to shape flat or slightly curved web surfaces, parts with simple bends or flanging holes, and can also replace drop forming for some applications. The forming of complex surface components must be done using drop forming or a composite process based on drop forming. Drop forming is a traditional sheet metal forming process in aerospace. It offers the advantages of simple equipment, ease of operation, and the ability to process parts with complex shapes and rapidly changing surfaces. However, it also has the drawbacks of significant noise pollution, extensive mold rework, unstable part quality, and low production efficiency.
To gradually reduce the use of drop forming, various aerospace manufacturers have partnered with universities to make significant advancements in hydraulic (liquid filling) deep drawing technology. However, most parts processed using hydraulic (liquid filling) forming are cylindrical, conical, parabolic, hemispherical, or other symmetrical, axisymmetric shapes with smooth profile transitions. In addition, complex parts such as mouth frames, bulkheads, gun covers, and reinforcing ribs are still formed using the drop press process. This study examines the applicability of stamping, widely used in the automotive industry, to the processing of complex aviation sheet metal components (aluminum alloy). Although aluminum alloy's cold forming performance is not as good as that of low-carbon steel or deep-drawing steel plates used in automotive applications, complex aviation sheet metal structures can still be formed if the appropriate forming process is chosen.
Stamping sheet metal components are typically processed using 2024 aluminum alloy, or similar alloys like LY12 and 2A12.
Wei Wang and colleagues' research shows that 2024 aluminum alloy exhibits excellent stamping performance. Biyan Zhao and others successfully processed and manufactured the launch vehicle fairing using 2A12 with mirror image deep drawing technology, achieving reliable dimensional accuracy, stable quality, and significantly improved production efficiency. Therefore, it is feasible to use stamping to form pressure-sensitive components such as mouth frames, gun covers, and reinforcing ribs, which cannot be formed using hydraulic (liquid filling) forming. To investigate the applicability of stamping in forming complex-surface sheet metal components for aviation, this study focuses on a typical mouth frame part from a specific model for analysis. First, three forming schemes were designed for the components. Then, finite element simulation software was used to simulate the forming process and analyze the results to identify the most suitable forming scheme. Finally, the forming tooling was designed and manufactured based on the analysis of the schemes.
This study examines a large mouth frame reinforcement part from a specific model, as shown in Figure 1. The raw material used for the part is 2024-O aluminum plate, with a thickness of 1.2 mm. The outer dimensions of the mouth frame reinforcement are 1000 mm × 500 mm × 100 mm, and it features a hyperbolic shape with several pairs of symmetrical reinforcement grooves and more than ten lightening holes of varying shapes and sizes. The presence of a reinforcement groove as deep as 15 mm makes it impossible to form the part using the skin-stretching process. Currently, the part is processed using multi-pass drop forming, with an annealing process between forming steps to relieve internal stress and reduce the risk of part rupture.
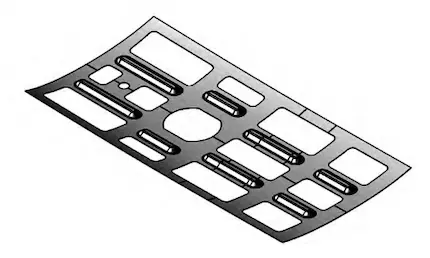
Figure 1 Mouth frame reinforcement
The following issues exist in the drop forming of the mouth frame part:
(1) The part's surface is hyperbolic with a small curvature. Significant rebound occurs after drop forming, requiring manual correction, which results in low production efficiency.
(2) The upper die of the drop hammer die is made from lead alloy, which has a large mass and low hardness. This causes the die surface to wear and deform easily during use, leading to poor surface quality and forming accuracy of the processed parts.
(3) During the forming process, the adhesion of lead and zinc heavy metals from the die to the surface of the part requires pickling after drop forming to remove these contaminants. If not removed, they can reduce the service life of the part. The additional processes increase the overall processing time of the part.