Problems such as spots, glossy spots or inconsistent gloss on
injection molded parts are typical appearance issues we encounter during our work, which may be affected by the mold or part design.
Let's start with the overall gloss of the part, as this is the easiest issue to address. If you have concerns about whether the entire part meets the requirement for appearance gloss, you can adjust the workmanship and materials. However, beyond that, you will also need to modify the surface finish of the mold steel.
In terms of processing, there are several options to try. Gloss can be affected by adjusting the mold temperature, feeding or holding pressure, filling speed, and material temperature. In most cases, these adjustments will not have a significant impact and will reduce the overall production process window, thereby increasing the possibility of other problems. Therefore, it is best to find the most suitable process for the part and maintain the finish of the cavity mold surface.
When dealing with the issue of gloss, don’t change the surface finish of the mold steel right off the bat. Instead, first adjust the process parameters to change the gloss of the product. Cooler molds, cooler melts, lower feeding or holding pressures, and slower filling rates can all make your plastic parts shinier. The reason for this is that with a cooler mold and less pressure applied, the plastic does not replicate the microscopic details of the mold steel surface finish. Conversely, higher mold and melt temperatures, higher feeding or holding pressures, and faster filling speeds will make your parts darker. The influence of melt temperature is not as significant as that of the filling speed, because the filling speed and the resulting shear force have a much greater impact on the material’s viscosity.
Each material provides a different gloss to the finished product. If the surface of the mold cavity has been polished, but the product’s surface gloss is relatively dark, consider increasing the polishing grade of the mold steel. However, if the mold steel has been polished to the highest possible grade and the product’s gloss is still not satisfactory, a process or material replacement is required.
If the product’s surface gloss is too high, consider reducing the polish of the mold steel surface or sandblasting the mold cavity. Both methods will create small pits in the steel, increasing the surface area, allowing the molded product to absorb more light, making the part appear darker, as shown in figure 1.
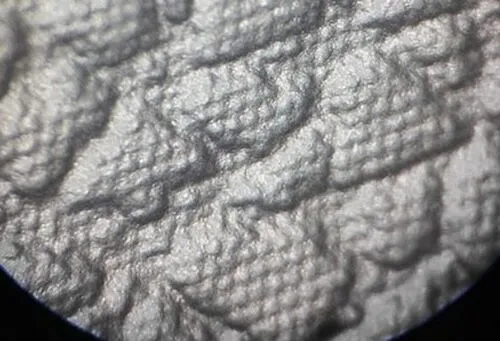
Figure 1 Small pits on the surface of the product reducing the gloss of the product
Another primary causes of gloss issues is the product’s design, particularly in areas where the wall thickness varies. Changes in wall thickness can make it challenging to maintain consistent glossiness across the part. Thinner wall sections experience less plastic pressure due to flow pattern variations, leading to higher gloss in this area. Insufficient discharge can also result in inconsistent surface gloss. Insufficient discharge can cause dark and light spots, depending on the materials and workmanship.
Gloss issues can also arise from inadequate cooling when certain areas of the cavity or mold assembly are hotter than others. In such cases, the product’s surface may appear brighter.
If a specific area of the part appears darker than the rest, especially in regions where too components like core pins or tappet rods are situate, those components should be inspected for distortion. This is particularly important when the part has a substantial cavity surface area. Excessive unsupported length and cavity surface area of ejector pins and tappet rods can cause plastic pressure to deflect the part.
Deformation forces on the mold parts exert stress on the plastic product, potentially resulting in a dull appearance. If the deflection of the mold deformation is small, it may be difficult to diagnose. However, in some cases, the effect of the plastic part being out of position in the mold can be clearly seen. If the gloss in this area is too high, first check the temperature of the mold components; if it is a temperature issue, there should be no obvious defects in the first molded product. If the corresponding area of the product in the mold part is dark, then the mold part should be checked for deformation.
Lamination can also cause gloss issue, which are usually easy to diagnose. Lack of venting, pooled materials, and cheap materials could all be contributing factors. When material buildup cannot be addressed, coatings can be used to reduce buildup and facilitate easier cleaning without affecting the gloss of the product.
Materials containing abrasive additives such as fiberglass can cause gloss issues by wearing down the surface of the mold cavity over time. In mold cavities containing texture, texture details can be eroded by abrasive additives over time, leading to an increase in the glossiness of the product. Using hardened mold steel or applying a hard coating can mitigate this problem and extend the internals between mold maintenance tasks.