German Industry 4.0 has reached a critical stage. It involves the automation of high-speed and precision stamping dies, the automation of high-speed and precision stamping machine tools and the selection of high-quality raw materials. China's high-speed cold stamping technology is constantly changing in the direction of digitization. High-speed precision automatic progressive stamping has significant advantages such as high efficiency, precision, safety, good quality and saving raw materials.
The SPM (referring to the stamping speed) of modern stamping equipment has been increasing year by year, not only good rigidity, high precision and reliability but also perfect automatic monitoring and protection functions must be ensured for the design of the punching machine. The stamping machine tool in our department adopts the advanced German design, which can guarantee the accuracy of the machine tool for a long time after the stress is relieved. In order to meet the requirements for high speeds, high precision and good rigidity of the punch press, high-speed progressive molds with high structure precision and excellent mold materials are required.
Most of the raw materials used in the stamping process are copper, pre-plated copper and stainless steel. Performance requirements of raw materials include mechanical properties, physical properties, chemical properties, corrosion resistance and other properties.
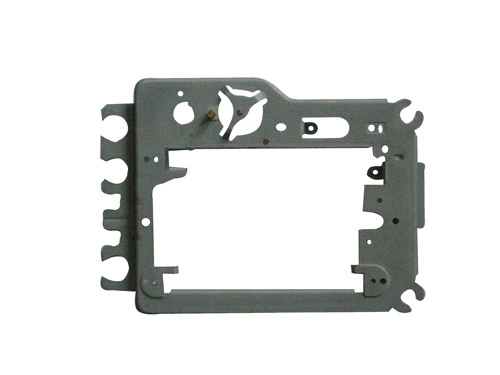
With the continuous progress and development of modern science and technology, customers have put forward higher requirements for the appearance of
stamping products, and there should be no crushing, dust, metal wire, etc. Moreover, the production should be carried out under high-speed states to ensure high-quality products. In addition to the high requirements for equipment, molds, and materials, there are also strict requirements on the production process. With the continuous development of manufacturing technology, in order to improve production efficiency, multi-station continuous stamping is increasingly applied to production practices of cold stamping. It also brings some technical problems that are different from traditional stamping. A jumping chip is one of them. If this problem can be solved well, the production efficiency of the stamping can be greatly improved.
With the continuous improvement of stamping speed, the appearance of some products is regular, resulting in a neat and simple waste design, and the problem of a jumping chip is very easy to occur in production. Jumping chips cause damage to the material belt, resulting in the poor appearance of the product. When it is more serious, the scrap will cause the mold to jam and damage the punch and knife-edge parts of the mold, which increases the time of mold repairs, affects the service life of the mold, and greatly reduces the efficiency of stamping. Well solve the problem of jumping chips can improve the product's quality, ensure the smooth stamping process and make sure that assembly and tests can be carried out on the assembly line successfully. In the manufacturing process, it is often found that the product will be crushed by some jumping chips of metal. As a result, batches of products are scrapped, which not only leads to a waste of manpower and material resources, but also fails to finish manufacturing the product before the delivery date required by customers. Therefore, we should pay enough attention to the jumping chip existing in the stamping process so that the stamping product can have better quality.